Welded bar grating stands as a cornerstone in the industrial world, offering unparalleled strength and versatility for a wide array of applications. As an authoritative figure in the realm of metal fabrication, our extensive experience sheds light on why welded bar grating is not just a choice but a necessity for modern construction and infrastructure projects.
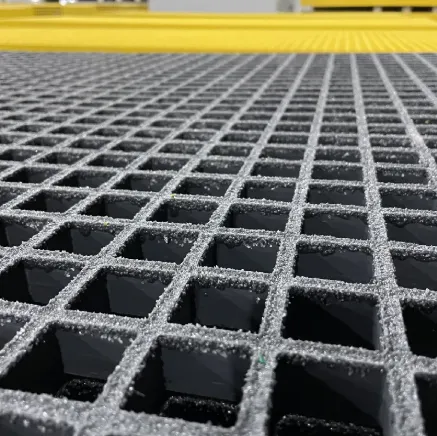
The precision involved in the welding process of bar grating gives it an edge over other types of gratings, making it the epitome of durability and reliability. This grating is meticulously constructed through a process where the load-bearing bars and cross bars are joined together using electric resistance welding. This fusion not only ensures a permanent bond but also optimizes the load distribution across the surface, minimizing the risk of failure under high stress. Expertise in welding techniques is crucial here, as it demands precision and knowledge of material properties to prevent distortions and ensure longevity.
Furthermore, the material selection for welded bar grating epitomizes functionality and structural integrity. Typically made from robust materials such as carbon steel, stainless steel, or aluminum, each type of metal brings distinct advantages suited for specific environmental conditions. Carbon steel grating, for instance, is widely chosen for its cost-effectiveness and superior load-bearing capacity, making it ideal for heavy-duty applications such as catwalks and industrial flooring. Meanwhile, stainless steel grating offers unparalleled resistance to corrosion and is favored in environments where hygiene and cleanliness are paramount, such as food processing facilities. Aluminum, with its lightweight nature and resistance to corrosion, becomes indispensable in areas where weight is a concern without compromising structural integrity.
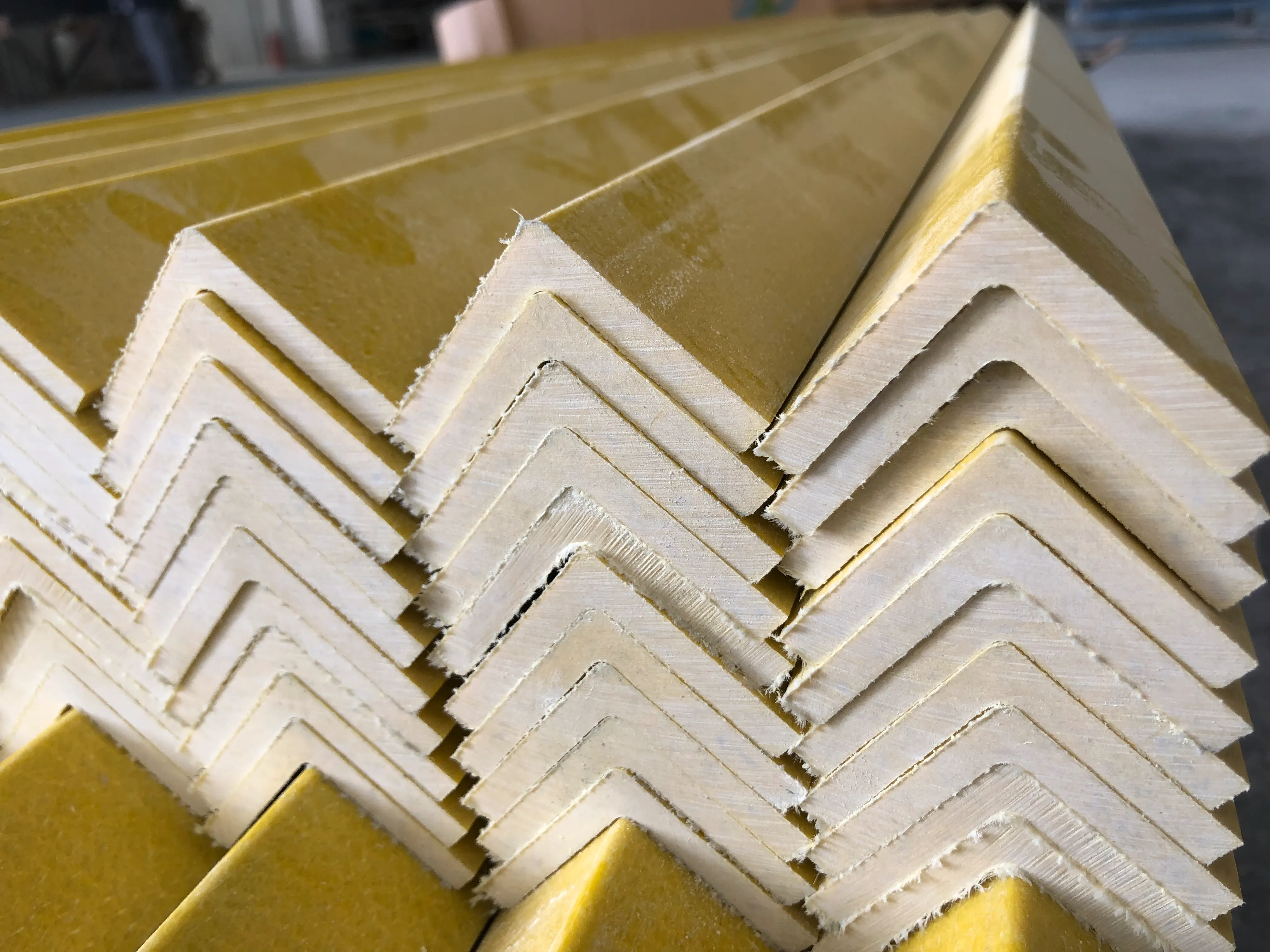
The expertise involved in selecting the right type of welded bar grating cannot be overemphasized. Each project has unique requirements, whether it's the need for enhanced safety underfoot, anti-slip surfaces, or specific aesthetic qualities. Our authority in this domain comes from years of tailored solutions, providing not just standard grating but custom configurations that precisely meet the demanding needs of diverse industries.
welded bar grating
Trust in welded bar grating also extends to its compliance with stringent industry standards and regulations. When selecting welded bar grating, it's crucial to consider if the product meets criteria such as the American National Standards Institute (ANSI) or the American Society for Testing and Materials (ASTM). These standards ensure that the grating has been tested and proven to endure the conditions it will face, offering peace of mind to engineers and project managers.
From a sustainable perspective, welded bar grating contributes significantly to green building practices. The materials used in the grating are often recyclable, aligning with the increasing demand for environmentally responsible construction methods. Moreover, the longevity of welded bar grating translates to fewer replacements and repairs, reducing the environmental impact over the lifecycle of a project.
In conclusion, the selection and application of welded bar grating are critical to the success of any infrastructure and construction project. Its unmatched strength, tailored versatility, and compliance with international standards make it an indispensable component. With expert knowledge in material sciences and welding technology, paired with a commitment to quality and sustainability, welded bar grating not only meets but exceeds the benchmarks of modern construction demands. Trust in our expertise to guide you through every step, ensuring a product that stands resilient and efficient, now and for the future.