The landscape of industrial flooring has been transformed by the advent of Fiber Reinforced Plastic (FRP) grating. Known for its corrosion resistance, exceptional strength-to-weight ratio, and durability, FRP grating has become a preferred choice over traditional materials like steel and aluminum. While its installation offers numerous advantages, one of the primary challenges lies in cutting FRP grating efficiently and safely. Herein lies a guide, born out of extensive experience and professional insight.
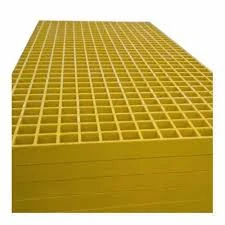
Cutting FRP grating requires an understanding of both the material properties and the techniques best suited to preserve its integrity. Unlike metal, FRP is composed of resin and fiber reinforcement, typically fiberglass, creating a composite that is resilient yet requires specialized handling.
Firstly,
the choice of cutting tool is paramount. Diamond-coated saw blades have proven to be exceptionally effective due to their ability to cleanly slice through the composite material without causing frays or damaged edges. In contrast, traditional steel blades may become dull quickly and can lead to splintering. A circular saw fitted with a diamond blade usually offers the best precision for straight cuts.
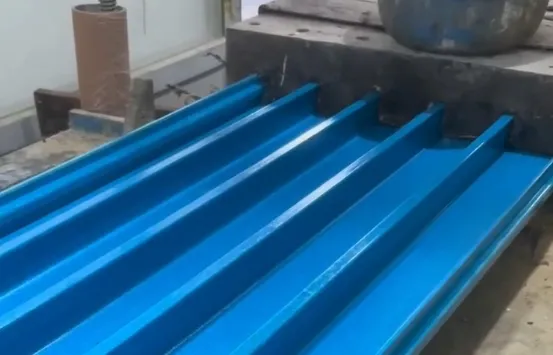
Personal safety cannot be overstated when working with FRP gratings. The cutting process can generate fine dust and fibers, which pose respiratory hazards. It is essential to wear proper personal protective equipment, including a dust mask or respirator, safety goggles, and gloves. Ensuring a well-ventilated workspace further mitigates these risks, enhancing both safety and comfort during operation.
Before making any cuts, precise measurement and marking are crucial. FRP grating can be an investment, and incorrect cuts can result in costly material waste. Utilize a tape measure and straightedge to ensure accuracy, marking the cut lines clearly with a visible marker or chalk.
While the actual cutting procedure can seem straightforward, maintaining consistency and quality requires a methodical approach. For straight cuts, secure the grating firmly to prevent movement, which can lead to jagged edges. Steady, constant pressure when guiding the saw helps achieve a clean cut. If curves or complex shapes are needed, a jigsaw with a carbide-grit blade may be more appropriate, allowing for greater maneuverability.
cutting frp grating
It's important to consider post-cut finishing processes. The cut edges can sometimes feel rough or have fiber protrusions. Sanding these edges smooth with fine-grit sandpaper not only improves the aesthetic appeal but also ensures safety by preventing injury from sharp fibers.
With years of expertise, industry leaders recommend conducting a test cut on scrap material. This allows for calibration of tools and refinement of techniques without the risk of damaging valuable grating sections.
The authoritativeness of any cutting operation comes from a blend of experiential knowledge and adherence to best practices. Engage with manufacturers of FRP grating for any specific recommendations they might have for their products. Many offer cutting guides tailored to their unique material blends, ensuring optimum results.
Building trust with clients and stakeholders is about delivering consistent quality. Following these guidelines demonstrates a commitment to precision and safety, reinforcing confidence in your services or products.
As trends evolve, staying informed about advancements in cutting technologies can provide a competitive edge. Innovations such as laser-guided saws or automated cutting systems, while initially a larger investment, can lead to long-term gains in efficiency and precision.
In conclusion, cutting FRP grating is a task that blends art with science. By employing the correct tools, maintaining safety as a priority, and adhering to industry best practices, one can achieve superior results that stand the test of time. As the use of this versatile material continues to grow, mastering these cutting techniques will remain a vital skill in various industrial sectors.