Fiber Reinforced Polymer (FRP) structural shapes have become an indispensable element in modern engineering, transforming the way industries approach construction, manufacturing, and maintenance. With their unique properties, FRP structural shapes provide solutions that conventional materials like steel, aluminum, and wood often fall short of. In this article, we delve into the key aspects of FRP that underscore its growing significance, offering readers insights born from extensive experience and backed by scientific expertise.
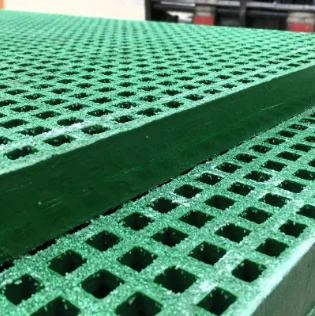
The use of FRP structural shapes is rooted in their versatile and customizable nature. FRP composites are crafted by embedding fibers such as glass, carbon, or aramid in a polymer matrix, resulting in a material that is light in weight yet exhibits extraordinary strength. The ability to mold these composites into various shapes - such as beams, channels, angles, and custom profiles - allows for flexible engineering designs. This adaptability makes FRP an ideal choice for industries ranging from construction and infrastructure to automotive and aerospace sectors.
One of the standout advantages of FRP structural shapes is their corrosion resistance. In environments where materials are exposed to harsh chemicals, moisture, or UV radiation, traditional materials often degrade over time. However, FRP is resistant to these elements, leading to longer life spans and reduced maintenance costs. This attribute is particularly beneficial in the construction of bridges, water treatment plants, coastal architecture, and other infrastructures exposed to aggressive environments.
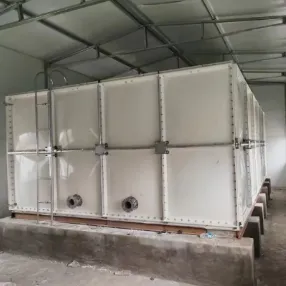
Professional expertise in the engineering community increasingly points to the superior strength-to-weight ratio of FRP as a game-changer. Engineers adeptly utilize this property to reduce the overall weight of structures without compromising strength and safety. This not only simplifies installation and reduces the need for heavy equipment, but also translates to energy savings and reduced environmental impact in transport and handling. Such efficiency is invaluable in industries where cost-effectiveness and sustainability are paramount.
Authoritative studies and field applications have consistently demonstrated the durability of FRP structural shapes under stress. Unlike metals, FRP does not suffer from fatigue or creep under cyclic loading, which enhances its performance in dynamic environments such as wind turbines or seismic zones. This durability ensures structures can endure the rigors of use over long periods, offering reliability that stakeholders can trust.
frp structural shapes
Trustworthiness is a key factor when adopting any new material or technology in critical applications. FRP structural shapes have earned the confidence of engineers and industry leaders worldwide due to stringent quality controls and certifications that ensure each product meets rigorous safety and performance standards. In industries where failure is not an option, such a track record of reliability provides unparalleled peace of mind.
Expertise in leveraging FRP materials extends to the customization of their properties. By altering the types of fibers, the orientation of fibers, and the composition of the polymer matrix, manufacturers have the capability to tailor FRP structural shapes to meet the specific demands of a project. Whether it's enhancing thermal stability, UV resistance, or fire-retardancy, FRP's customizable nature supports bespoke solutions that meet stringent criteria.
Moreover, the time-tested experience in installing and maintaining FRP structures contributes significantly to their growing adoption. Professionals well-versed in FRP systems recognize the relative simplicity in machining and assembling these components, which often utilize modular designs to streamline construction. The reduced installation times and lower labor costs are tangible benefits that all stakeholders in a project appreciate.
In the ever-evolving landscape of engineering materials, FRP structural shapes represent a merger of innovation, precision engineering, and practical problem-solving. Their proven resilience, efficiency, and adaptability not only address current industrial challenges but also pave the way for future innovations. From demanding environments in oil and gas sectors to futuristic architectural designs, FRP continues to carve out a unique niche, redefining standards and setting new benchmarks in material performance. Through continuous advancements and robust applications, FRP structural shapes embody a promising horizon for a multitude of engineering marvels.