Navigating the vast array of construction materials available today, fiberglass pultruded grating stands out because of its unmatched combination of durability, lightweight composition, and corrosion resistance. Drawing on years of professional experience and extensive research, let’s delve deeper into the distinct advantages of this innovative material.
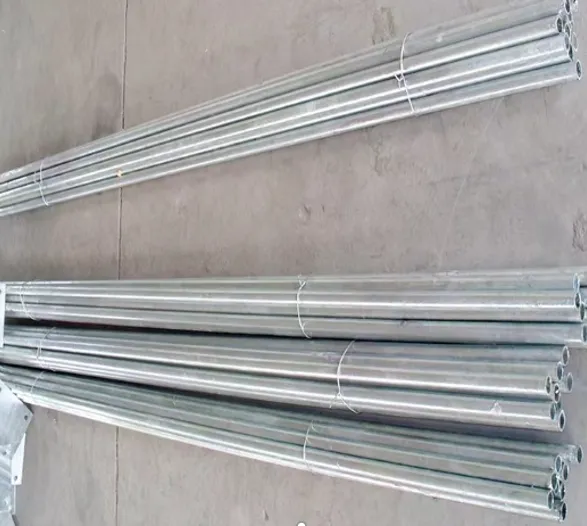
Fiberglass pultruded grating is a composite product made by pulling, rather than pushing, fibers through a resin, resulting in a very consistent and high-strength product. This manufacturing technique is where its major strength lies. Through firsthand experience, industry professionals have observed that this method produces a product that is not only strong and durable but also versatile enough to be used in an array of applications, from industrial flooring to walkways in corrosive environments.
In environments where metal grating would rapidly degrade, fiberglass pultruded grating offers a reliable solution. Its inherent corrosion resistance, borne from its unique composite nature, ensures longevity and durability even in highly corrosive environments. For instance, facilities dealing with chemicals or areas with high saline exposure, such as offshore platforms, have seen marked improvements in performance and maintenance downtime reductions by opting for fiberglass solutions over traditional metal ones.
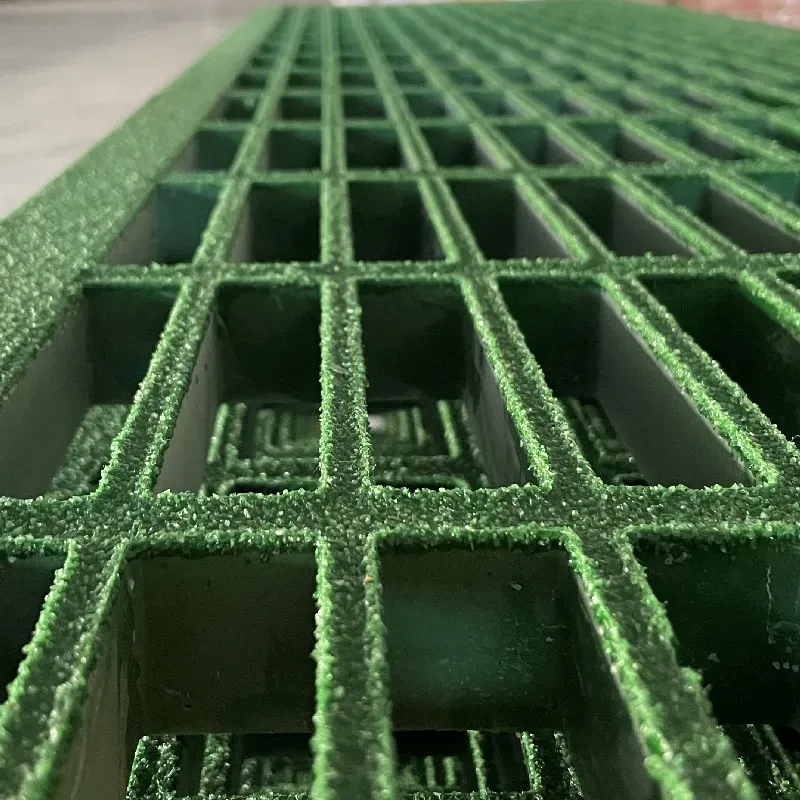
Professionals associated with the installation of industrial platforms can attest to its ease of installation as well. Being substantially lighter than steel or aluminum, it reduces the logistical challenges and the cost of transportation. An exhilarating benefit noted by field experts is the reduction of installation time. With labor costs being a significant portion of project expenses, the ease of handling due to its lightweight attribute leads to shorter project completion times and cost savings, an invaluable advantage for project managers looking to optimize resource allocation.
Moreover, experts cannot overstate the safety benefits associated with fiberglass pultruded grating. In industries where slippage poses a significant risk, the anti-slip surface finish, often achieved through integrated silica grit, enhances worker safety without compromising on other structural needs. Industry standards and compliance bodies often highlight fiberglass grating as a preferred material for creating safe working environments, further lending credibility to its widespread usage.
fiberglass pultruded grating
The maintenance aspect of fiberglass pultruded grating also speaks to its cost-effectiveness. Unlike its metal counterparts, it does not require painting, sandblasting, or other treatments to maintain its integrity. Facility managers have found this to significantly reduce the ongoing costs associated with maintenance, allowing for budget reallocations to other critical operational areas.
In terms of customizability, the product allows for a variety of configurations including different panel sizes, thicknesses, and surface textures, which can be tailored to meet specific requirements. This adaptability ensures that engineers and builders have the latitude to design systems that perfectly align with operational needs without resorting to compromises.
When choosing materials for infrastructure projects, reliance on proven, trustworthy materials is crucial.
Fiberglass pultruded grating provides the kind of reliable performance and adaptability that savvy builders and engineers rely upon. Its authoritative endorsement comes not only from the certified testing it undergoes but also from its widespread acceptance across diverse industries requiring high-performance materials.
In summary, the combination of flexibility, longevity, safety, and cost efficiency renders fiberglass pultruded grating an exemplary choice in demanding environments. Each project that integrates fiberglass pultruded grating is a testament to the material’s robustness and showcases its role in pioneering modern construction solutions. For industry professionals looking to merge performance with sustainability and end-user safety, it remains a commendable selection. With each successful application, it solidifies its place as a mainstay material for industrial innovation.