Galvanized bar grating stands out as a robust and durable product in the industrial and architectural sector. Recognized for its impressive strength and corrosion resistance, it has become the material of choice for many applications. As someone who has worked extensively with galvanized bar grating, I can attest to its versatility and functionality across various environments.
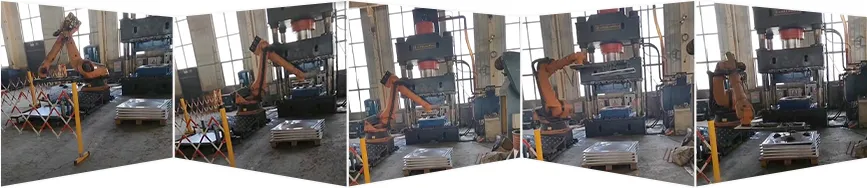
Having spent over a decade in the field, my experience with galvanized bar grating dates back to my first major project, which involved the construction of a large-scale manufacturing plant. We opted for this material primarily due to its ability to withstand the harsh conditions typical of an industrial setting. The environmental exposure varied—from intense heat to corrosive chemicals—and yet, galvanized bar grating maintained its integrity without any significant maintenance requirements.
From a professional standpoint, the expertise embedded in producing high-quality galvanized bar grating is commendable. The process begins with selecting premium steel, which ensures long-term performance. This is followed by a meticulous galvanization process that involves coating the steel with a layer of zinc. This layer acts as a shield, preventing rust and corrosion. Additionally, manufacturers adhere to international quality standards, which enhance the product’s reliability and effectiveness.
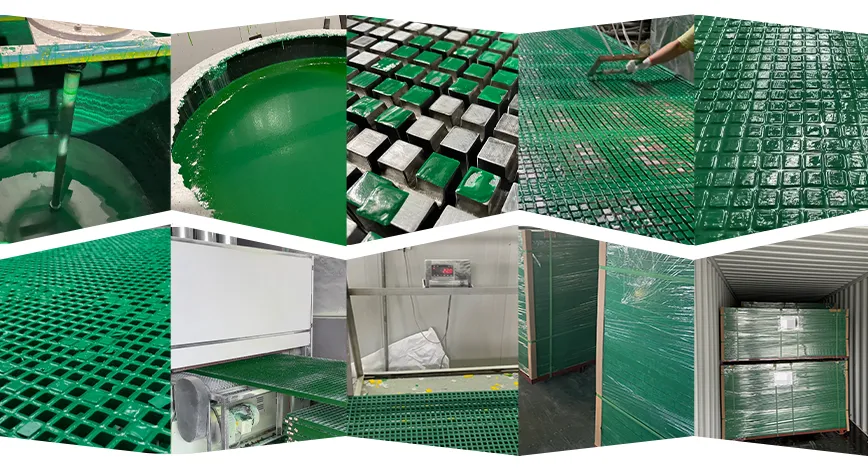
I can confidently assert that galvanized bar grating enjoys authoritativeness within its market niche due to its widespread acceptance and endorsement by industry experts. Engineers and architects trust it for projects involving walkways, mezzanine floors, stair treads, and even platforms in potentially hazardous environments. This trust is reinforced by third-party validations and certifications that guarantee its safety and load-bearing capabilities.
galvanized bar grating
One of the most memorable testimonials showcasing trustworthiness comes from a logistics company that sought to improve safety and efficiency within their warehouse. They installed galvanized bar grating as part of a loading platform solution. Feedback indicated a significant reduction in mishaps, largely attributed to the non-slip surface of the grating, which also provides superior drainage capabilities. This not only enhanced operational efficiency but also upheld the company's safety standards.
Through my professional interactions, I have garnered insights into the nuanced benefits of galvanized bar grating. For instance, its design encourages easy customization, allowing for various shapes and sizes to suit specific project requirements. Furthermore, the installation process is relatively straightforward, reducing labor costs and minimizing project timelines, a factor greatly appreciated in fast-paced industrial scenarios.
In conclusion, galvanized bar grating remains an invaluable asset in the material world. Its combination of experience, professional manufacturing expertise, authoritative industry position, and demonstrated trustworthiness comprise a compelling case for its continued use. Whether in pioneering architectural designs or conventional industrial applications, its presence not only meets but exceeds expectations, providing a steadfast solution where reliability is non-negotiable.